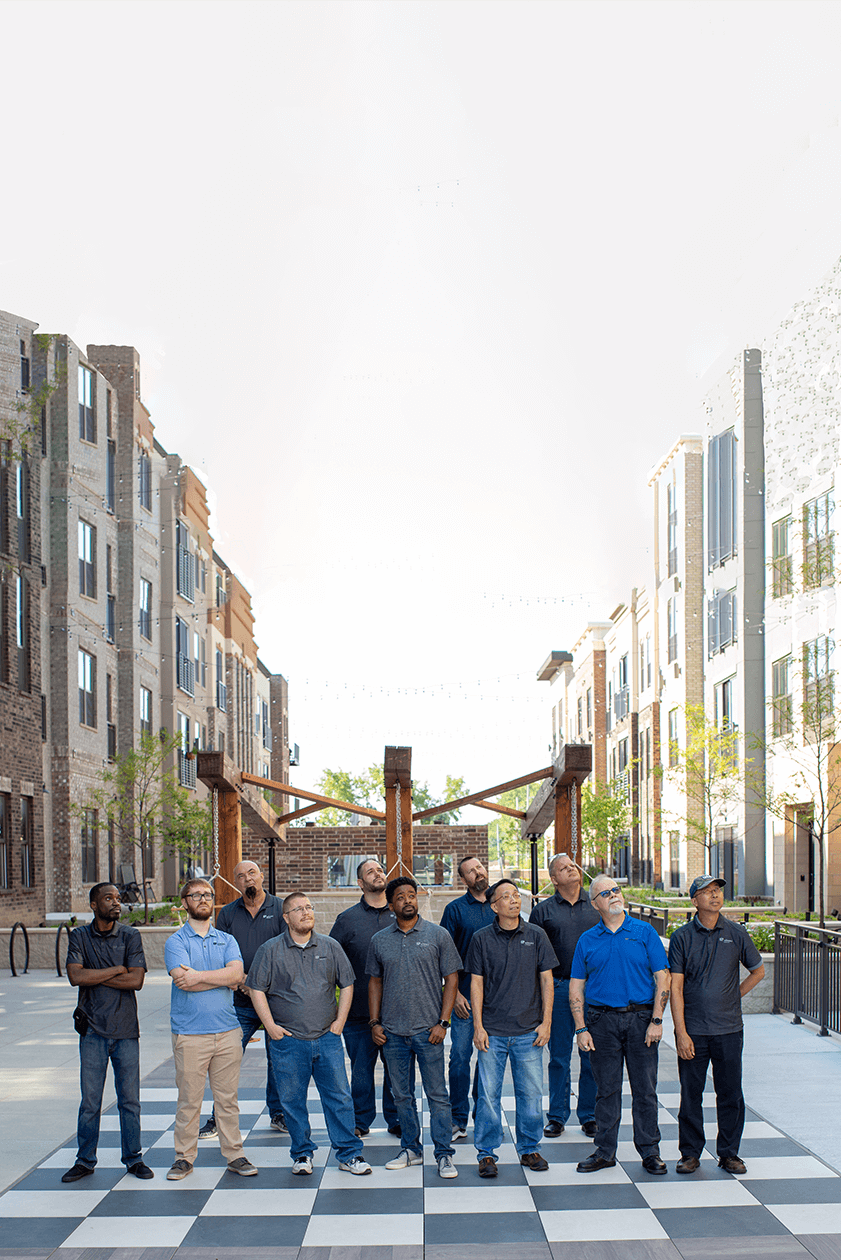
The Emergency in Marion, Ohio
Infrastructure
TRG-Royal Bay was experiencing issues with a display manufacturing and assembly program they were running for a large distributor. The display housed a large volume of smaller items which were being unpacked and added to the displays as part of the process. The customer required that serial numbers be reported back for them at multiple levels, and the serial numbers for each display, as well as the ID for the display needed to be able to be tracked by display after shipment. TRG-Royal Bay was initially tracking this information on spreadsheets, and at several points during the process, product serials got mixed up within the shipments, and some serial numbers were duplicated because of the large volume of products being added and removed from the displays, and the speed at which displays were being produced. They had additional display jobs they were going to be working on and were discussing other display programs with even more data capture and reporting requirements from other customers. They deemed the current state of operations unacceptable for the existing customer requirements and those of other potential work, and contacted our team for assistance.
Scroll down to read how we solved their problem!
Download PDFSolution:
We were able to repurpose code from a smaller application to build out a larger solution to manage multiple levels and types of serial codes required in the displays. Using bar code scanning to capture the data within the application, the tracking number on a pallet (the license plate) tied shipments to displays, and displays to all the serial numbers within.
To provide a better level of QA and validation for those parts being added and removed (the ones that had caused so many problems before), we required products to be scanned in and out of a display and provided visual feedback to the people building the displays. This not only ensured correct counts but made sure the right codes and products were being scanned. The SCOT application would provide visual reporting to show that the correct amount of product was being scanned in and out of each display and provide “Red Light” alerts, based things like, duplicate serial numbers, the same serial accidentally being scanned multiple times, or failure of a code “Type” check—to make sure someone didn’t accidentally scan a the UPC instead of the serial number on the product.
Once we were capturing good, validated data, we were able to provide a more detailed level of reporting by using SCOT in conjunction with the data in TRG’s WMS system to assist in customer support and in their reporting requirements. Building this web application reduced effort, enforced accuracy, increased speed, enhanced quality, and increased customer satisfaction. We can now re-configure and customize this application for other requirements within the Schwarz Partners family of companies, and incorporate as a module or function in even larger scale applications.
Process:
Working with TRG we determined the initial requirements and suggested additional enhancements & efficiencies that we could add in the required timeframe. This was a good opportunity for us to review and enhance some existing code we had built for SPA (another TRG fulfillment center.) The original SCOT program was used to capture serial numbers at time of shipment for boxes of pre-activated software packages being shipped to big box retailers. In the event of theft, or software activation codes being used before the product was sold at the retailer, the scans from SCOT could be used to find the shipments and locations the product went. The software manufacturer and/or the retailer could look at the shipments and isolate where the potential breach had occurred.
After building out the initial requirements for the proof of concept, we worked with TRG to expand and enhance functionality. We also built test scenarios, allowing us to get updates to TRG to validate the changes they required with less repeated testing on their part.
This application has been working for multiple TRG display programs, during which we have added additional functionality and reporting. We see this application expanding its use throughout the Schwarz Partners family of companies.